Conveyor Optimization: The Technical Excellence of Our Idlers and Rollers. Optimizing conveyors is pivotal for ensuring both profitability and safety in material transport. Within this context, idlers and rollers emerge as critical components that directly influence the performance of conveyor systems. Their careful selection and proactive maintenance are paramount to the success of material handling operations. One of the primary considerations is reliability, as it directly impacts conveyor downtime. A reliable conveyor system minimizes interruptions, enhancing the overall efficiency of material transport. This reliability also translates to a positive impact on working conditions through noise, dust, and spillage reductions, contributing to a safer and more comfortable environment for workers. Environmental considerations are equally important in conveyor optimization. By minimizing waste and maximizing efficiency, conveyor systems can contribute significantly to sustainable practices. This not only aligns with GES responsibilities but can also lead to cost savings by reducing material waste. RELIABILITY, FIRE-RETARDANCYConveyors serve as vital links between different processes, making their efficiency crucial for overall productivity and cost-effectiveness. Rollers, being the most abundant components of a conveyor system, play a pivotal role. Opting for more reliable, fire-retardant, and longer-lasting rollers not only reduces downtime and maintenance frequency but also substantially enhances the profitability of the entire material handling operation. ENDURIDE’S PATENTED TECHNOLOGIESEnsuring the longevity and optimal performance of conveyor roller bearings is paramount, especially in industries where downtime translates to substantial financial losses, such as mining and ports. The reliability of conveyors directly influences operational efficiency, maintenance costs, and overall production output. In response to these critical needs, our patented Triple-Labyrinth system and Ultim8 technologies stand out by providing unparalleled protection for bearings in abrasive applications. This innovation enables end-users to rely on equipment that is not only robust but also minimizes unplanned downtime to a significant extent. Moreover, our commitment to innovation extends to a patented Roller assembly, further reinforcing the reliability and efficiency of conveyor systems. As a comprehensive solution, we have integrated a superior sealing system into our Ultim8 rollers, elevating their reliability to a remarkable 25 times that of standard rollers. Our sealing system is strategically designed to address the primary causes of bearing failure, including contamination, external vibrations (mitigated by the polyurethane acting as a damper), and impact or shattering. This multi-faceted approach ensures that our rollers not only endure the challenges posed by abrasive environments but also remain resilient in the face of adverse conditions that typically lead to bearing failures. 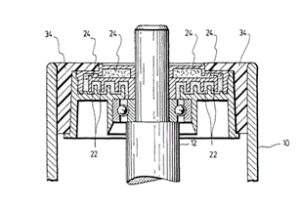 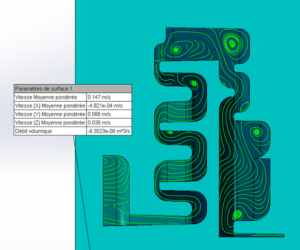
Our patented technologies go beyond conventional solutions, offering a level of protection that significantly enhances the lifespan and reliability of conveyor roller bearings. This, in turn, translates into enhanced operational efficiency, reduced maintenance costs, and optimized overall production for our valued clients in industries where downtime is a costly adversary. ADDRESSING ABRASIONThere are two main causes for roller replacement: seizure and shell wear. Seizure is caused by ineffective sealing, incorrect bearing sizing, bearing grease contamination and excessive deflection. As for roller shell wear, this is influenced by the abrasive nature of the materials conveyed, as well as by roller alignment and blocking. If left untreated, this wear can damage the belt. It also has an impact on conveyor maintenance, resulting in downtime to replace worn rollers. This increases the consumption of these components and requires more workforce to replace them. ADVANTAGES OF UHMW IN CONVEYOR ROLLERSUHMW (Ultra High Molecular Weight) polymer has several properties that make it highly sought-after in many industrial applications. ENDURIDE has mastered its use by adding a 12.7 mm (0.5 inch) layer to the steel tubes of its conveyor rollers and offering the option of a 0.01-inch TIR. This optimizes conveying operations: - Abrasion resistance: UHMW is renowned for its high resistance to abrasion, making it an ideal choice for parts in contact with rough or abrasive surfaces.
- Chemical resistance: It is resistant to many chemicals, making it suitable for industrial environments where aggressive chemicals are present.
- Low coefficient of friction: UHMW has an exceptionally low coefficient of friction, reducing friction and wear.
- Reduced material build-up: The UHWM coating creates a smooth, non-stick surface that prevents bulk materials from accumulating or sticking to the rollers for a smoother flow and greater efficiency in conveying operations.
- Low moisture absorption: It absorbs truly little moisture, making it suitable for applications in humid environments.
Life is up to 6 times longer than a conventional one! When the steel tube appears, it is time to change it. CUSTOMIZATION BEYOND COMPAREEnduride stands out as a pioneer in the conveyor industry by embracing a level of customization unparalleled by other major players. Unlike our competitors, we offer end-to-end customization, catering to the unique needs of each customer. Our commitment to tailoring solutions from A to Z sets us apart in the industry. Our customization capabilities extend beyond the ordinary. We actively collaborate with our customers, working together to adapt our solutions to their specific operational requirements. This includes seamless retrofitting into existing idler systems and the ability to design and produce custom solutions on demand. 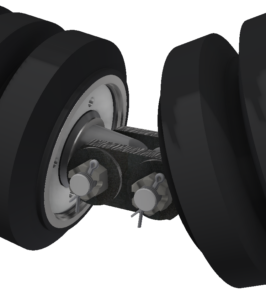
Recognizing that every customer brings distinctive needs, challenges, and preferences to the table, we pride ourselves on our willingness to delve into customization for individual clients—a rarity in the conveyor industry. At Enduride, we understand the value of crafting solutions that align precisely with the requirements of each customer, an aspect often overlooked by other conveyor roll companies. LOW QUANTITIES FOR TESTING PURPOSESWhether it is tailoring combinations of application, surface material, shaft material, or seal type, we go the extra mile to meet your exact specifications. What truly sets us apart is our flexibility, even accommodating low quantities for testing purposes. Enduride is dedicated to delivering what others simply cannot—providing a level of customization and adaptability that defines a new standard in the conveyor industry. PERSONALIZED CONSULTATION AND OBSERVATIONWhat distinguishes our approach from other solution providers is our unique ability to pinpoint and address not only the symptoms related to a faulty idler but, more critically, to unearth the root cause of our client’s challenges. Often, the idler is just a component affected by a larger issue, such as design flaws, application discrepancies, or environmental factors like impacts, fall points, or ore overflow. While our high-quality idlers can certainly enhance the situation, we recognize the necessity of delving deeper to offer comprehensive solutions. Our consultation process is grounded in a thorough examination of the working and operational environment, allowing us to address specific needs such as falls and troughing precisely. Internally conducted expertise on rolls, including failure analysis and simulation, forms the cornerstone of our approach. In our detailed failure analysis and consultation services, we meticulously explore several types of failures that can impact conveyor systems. These include surface abrasion, bearing failures attributed to contamination, and issues arising from the under-sizing of components. By scrutinizing these failure types, we ensure a comprehensive understanding of the challenges our clients face, enabling us to provide tailored solutions that go beyond surface-level issues, resulting in a more robust and effective material handling system. We don’t just aim to sell more rollers to our clients; rather, our focus is on assisting them in reducing the overall number of rollers required, thereby optimizing conveyor availability. We position ourselves not merely as suppliers but as partners in problem-solving, providing integrated solutions that go beyond idlers, incorporating our Brunone solutions. This commitment to a comprehensive approach is what is often missed, and it underscores our dedication to delivering value by resolving the core issues our clients face in their material handling processes. TAILORED EXCELLENCEOur mission at Enduride goes beyond merely supplying conveyor components – we are dedicated to crafting the optimal solutions for your unique needs. We follow a dynamic three-step approach: firstly, understanding your specific requirements; secondly, suggesting customized solutions tailored to address those needs comprehensively; and thirdly, actively tracking and implementing improvements over time. What truly sets us apart in this industry is our commitment to customization, a unique feature in our sector. The ability to adapt and tailor our solutions according to your operational realities is our forte. Moreover, our response time to address any issues you may encounter with our products is exceptionally swift. At Enduride, we do not just offer components; we provide a responsive partnership, ensuring that your conveyor systems not only meet but exceed expectations. Your success is our priority, and we stand ready to continuously enhance and optimize your material handling processes. |