METAL7

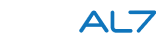
DDRF-S: Enhanced plant capacity with minimum investment.
Are you seeking to boost the production capacity of your pelletizing plant without making significant capital investments? How about reducing our carbon footprint? Read on for valuable insights!
Motivation
Most pelletizing plants look for solutions to increase plant capacity and reduce energy consumption. To achieve this, operators usually look at increasing the capacity of the indurating machine as an option. However, such a decision means bigger budgets. There is a smarter way to achieve it, the use of a segregated pellet bed profile promotes improvement on the air permeability in the induration furnace, improving plant throughput and/or reducing energy consumption, with an important impact on carbon footprint.
The solution
Metal7 excels at improving existing solutions, so it always keeps its promise: helping our clients meet their performance goals and contribute to its roadmap towards decarbonization by reducing energy consumption.
SAME FOOTPRINT
Instead of increasing the capacity of the indurating furnace, Metal7 proposes an improvement on pellet bed permeability. Metal7’s Double Deck Roller Feeder Segregation (DDRF-S) solution was designed to increase the screening area for the same footprint, improving the screening efficiency and promote a segregated pellet bed in the firing process.
UNIFORM PARTICLE SIZE DISTRIBUTION
Improving pellet bed permeability is the feasible way to reduce pressure drops throughout the induration process. It is the key factor in finding extra capacity in the current process fans at a low CAPEX investment.
DOUBLE DECK, SEGREGATION, LOWER ENERGY CONSUMPTION
Metal7’s DDRF-S allows pellets to be fed to the induration furnace on a bi-layer bed with the largest pellets on the top and the smallest ones on the bottom. Since bigger pellets are more difficult to fire, using a segregated bed allows the warm air that descends in the firing zone of the induration machine to transfer its maximum heat content to the biggest pellets first, precisely where it is most required. On the bottom layer, the remaining available energy handles the smallest pellets, which are much easier to fire.
Metal7’s patented Epsilon Chute reduces the impact force when the pellets are loaded into the furnace, so the sphericity of the pellets and the uniformity of the loads are improved. This is a key element to improving permeability.

BENEFITS & FEATURES
- Concept of segregation.
- Better gas flows through the pellet bed.
- Increased induration furnace capacity typically 7.5%.
- Improved balling process efficiency and increased productivity.
- Improved pellet quality in the range of 2 to 18% for physical and metallurgical properties.
- More uniform pellet size distribution.
- Smarter use of energy in the firing zones.
- Energy saving up to 15%.
- Green house emission Reduction.
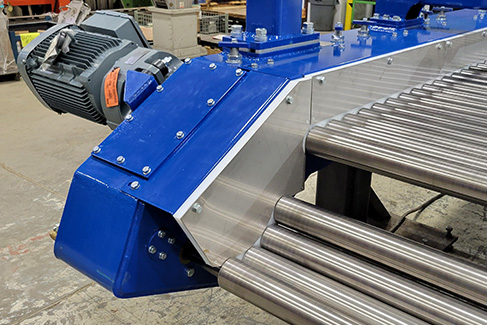
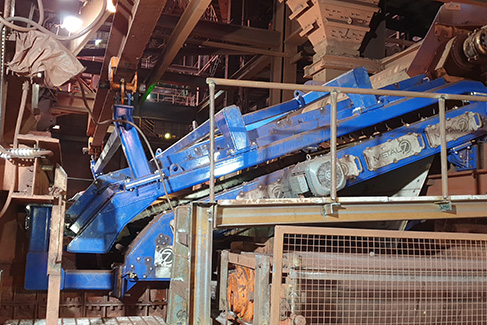
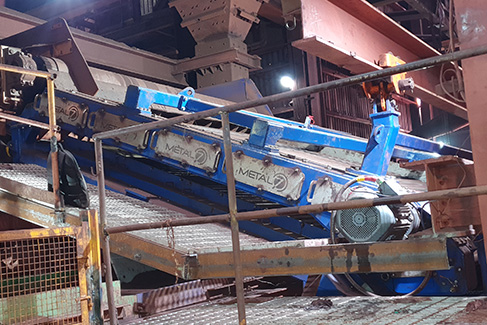
Further information
We understand that some topics may be more complex and raise specific questions that may not be fully covered on our site. If you have more specific questions, special requests or require further clarification, we strongly encourage you to contact us.