METAL7

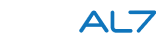
DDRS: The future of the screening process is now available.
Unlock the future of efficiency in pelletizing plants with Metal7’s groundbreaking Double Deck Roller Screen. It ingeniously expands your screening area within the same space as a Single Deck Roller Screen, pre-screening larger particles, potentially boosting capacity of agglomeration units by up to 20%, all while optimizing pellet quality. Metal7’s exclusive technology not only provides this but also offers a straightforward means to reduce greenhouse gas emissions by ensuring a more uniform pellet feeding the induration furnace. This enhancement in bed permeability can lead to energy consumption reductions, equivalent to removing up to 6,000 cars from the road in some cases.
Motivation
Numerous iron ore pelletizing plants seek ways to enhance their capacity. One approach is to decrease the recirculating load on the green pellet circuit while maximizing the proportion of good-sized pellets in the final product. While many solutions focus on the balling equipment to achieve a narrower pellet size distribution, the screening process plays a crucial role in enhancing screening efficiency and firing processes, resulting in a higher proportion of on-size pellets in the final product.
The solution
The DDRS (DOUBLE DECK ROLLER SCREEN) was developed with a primary aim of significantly increasing the screening surface. Compared to the SDRS (SINGLE DECK ROLLER SCREEN), it enhances process efficiency within the same footprint. By adding a deck above the lower deck, the DDRS pre-screens the larger particles, retaining larger ones on the top deck while allowing pellets smaller in diameter to pass through the gap openings and enter the fines removal zone on the lower deck. The material held in the top deck later falls onto the lower deck to complete the screening process. Through Discrete Element Method (DEM) simulations involving various process flowcharts, including balling disc, and balling drum circuits, it has been demonstrated that the DDRS offers benefits in plant throughput and/or particle size distribution.

BENEFITS & FEATURES
- Increased screening surface, promoting better screening
- Pre-screening of larger particles.
- Significant reduction of the recirculating load.
- Increased plant capacity.
- Reduction on carbon footprint in the induration furnace, so reduction of emission associated to Scope 1.
- Added flexibility to the process, due to increase in plant throughput.
- Sliding top deck for easier maintenance.
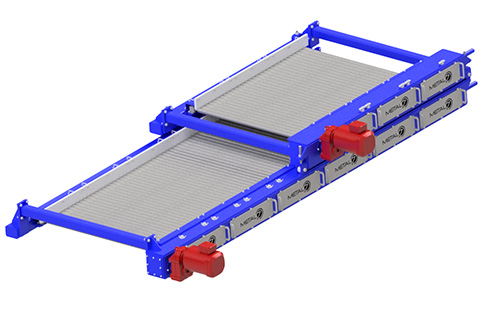
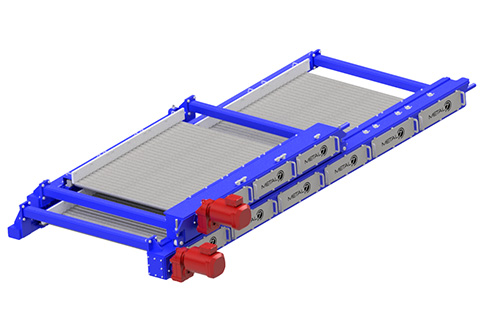
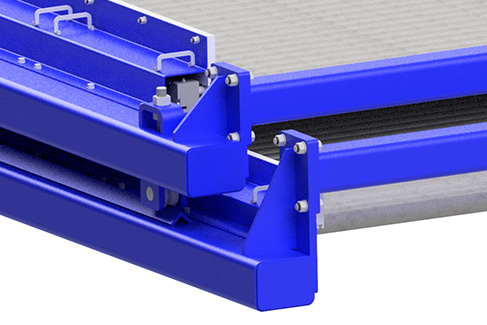
Further information
We understand that some topics may be more complex and raise specific questions that may not be fully covered on our site. If you have more specific questions, special requests or require further clarification, we strongly encourage you to contact us.