METAL7

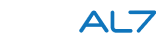
SDRF: Optimized Pellets Screening Efficiency.
Upgrade your pellet plant’s performance with Metal7’s Enhanced Single Deck Roller Feeder, optimizing screening efficiency, reliability, and maintenance ease for superior pellet production.
Motivations
You know that a roller feeder unit is a critical equipment in iron ore pelletizing plant operation. This screening unit processes the agglomerates produced by the balling process by removing fines and broken pellets. It ensures that uniform on-size pellets are spread on the pallet car of the induration machines. It is naturally linked to the induration furnace and balling process, which drive performance. Screening efficiency impacts not only the material being fed to the furnace, but also the balling operation. The Single Deck Roller Feeder has been used in iron ore pelletizing plants for decades. Our team took this well-known technology and improved its design to make it more efficient and reliable.
The solution
Over the years, Metal7 has continuously improved its Single Deck Roller Feeder (SDRF) design by focusing on key processes and operational parameters:
- Maximize screening efficiency.
- Improve reliability.
- Ease maintenance teams’ activities.
PROPRIETARY WEAR-RESISTANT ROLLERS COATING
Metal7’s proprietary wear-resistant coating maintains the rollers’ shape and gap uniformity over time, optimizing screening efficiency. It also improves transport of pellets over the rollers , avoiding material build up.
SPRING-LOADED TENSIONER AND CONSTANT LUBRICATION
The drive case comes sealed and pressurized to prevent foreign contamination. Metal7 also designed it with a chain guide and spring-loaded tensioner to provide optimal tension in the chain system. The oil bath is located at the discharge end of the drive case for constant lubrication of mechanical components. This straightforward design of internal components allows for quick, safe, and easy maintenance.
ROLL BLOCK AND SKIRTING SYSTEMS
The equipment is also designed with a roll block system (idler side bearing) that secures rollers in place, reduces vibration, speeds up gapping procedures and roller replacement activities. The improved bearing sealing system reduces contamination, improving lifespan. The skirting system is designed with adjustable sliding inserts to allow a flexible gap strategy.

BENEFITS & FEATURES
- Maximum screening efficiency over time.
- Fewer shutdown periods for gapping and roller replacement.
- More uniformity in the gap openings.
- Flexible gap strategy.
- Variable deck angle.
- Variable rollers rotation speed.
- Rollers wear resistant coating to improve lifespan and process overtime.
- Roller’s length is between 1,000 to 6,000 mm.
- Roller’s diameter between 83 to 200 mm
- Chain driven system.
- Individual motor drive system available.
- Straight deck, broken nose or Metal7 patented Epsilon Chute.
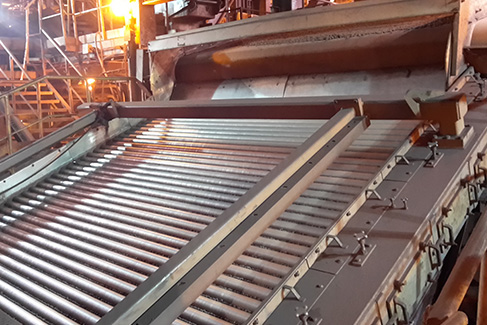
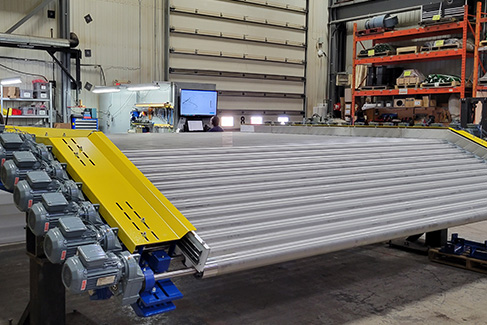
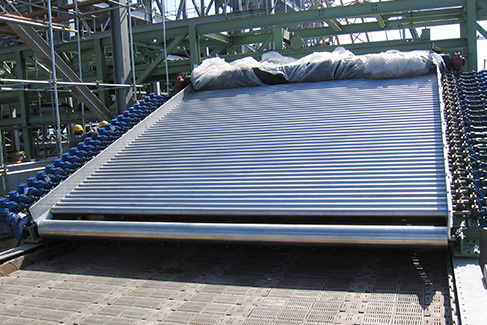
Further information
We understand that some topics may be more complex and raise specific questions that may not be fully covered on our site. If you have more specific questions, special requests or require further clarification, we strongly encourage you to contact us.