METAL7

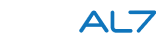
Roller Screen
The first iron ore pelletizing plants used vibrating screens to separate the over and undersized pellets from the good-sized ones. In the 1960s, vibrating screens were replaced with roller screen technology, revolutionizing iron ore pelletizing at the time. This technology is also a more efficient alternative to vibrating screens for other screening applications. Metal7’s roller screen technology plays an essential role, screening over 250 million tons of iron ore pellets every year.
SDRS
Single Deck Roller Screening
The single-deck roller screen is used to remove fines and oversized pellets from agglomeration units. This Metal7 technology is world-renowned for its robustness and manufacturing quality – your key to excellent screening efficiency in heavy-duty applications.
Key benefits:
- High screening efficiency.
- Robust, high-quality manufacturing.
- Rollers with protective anti-wear and anti-sticking coating.
- Simple, precise adjustment for a multitude of gap openings between rollers.
- Minimized downtime.
- Easy maintenance.
- Reduced recirculating load – less rejections, more productivity.
- More uniform pellet size in the finished product – improved quality.
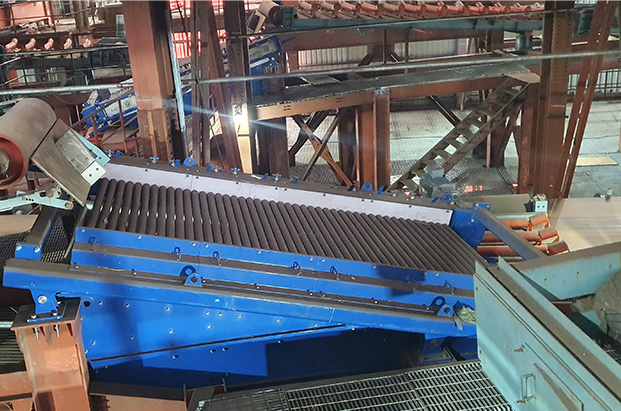
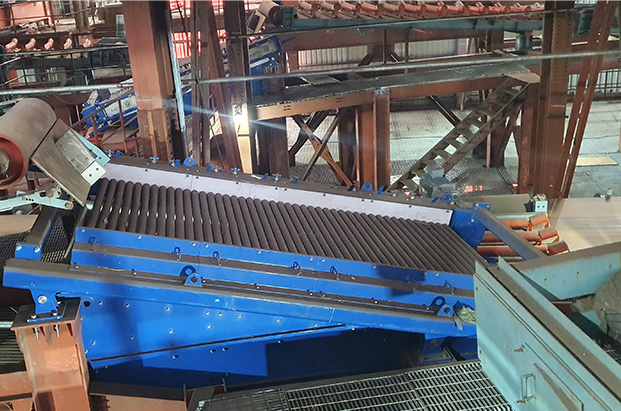
SDRS
Single Deck Roller Screening
The single-deck roller screen is used to remove fines and oversized pellets from agglomeration units. This Metal7 technology is world-renowned for its robustness and manufacturing quality – your key to excellent screening efficiency in heavy-duty applications.
Key benefits:
- High screening efficiency.
- Robust, high-quality manufacturing.
- Rollers with protective anti-wear and anti-sticking coating.
- Simple, precise adjustment for a multitude of gap openings between rollers.
- Minimized downtime.
- Easy maintenance.
- Reduced recirculating load – less rejections, more productivity.
- More uniform pellet size in the finished product – improved quality.
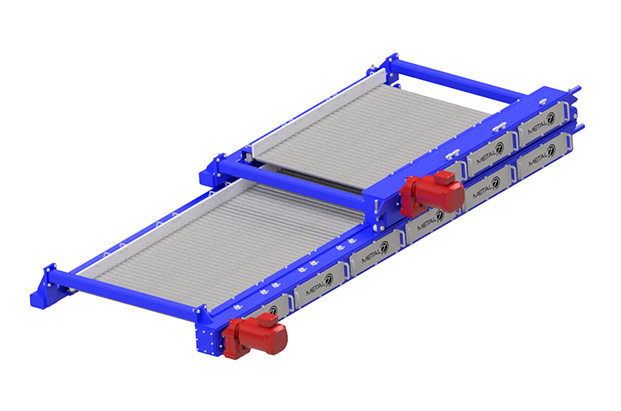
DDRS
Double Deck Roller Screening
A breakthrough for the agglomeration circuit! The combination of an enlarged screening surface and pre-screening is the key to dramatically improving screening efficiency. Replacing the traditional single-deck roller screen (SDRS) with our exclusive Metal7 double-deck roller screen will offer considerable advantages.
Key benefits:
- Same reliability and manufacturing quality proven on the SDRS model.
- Compact design to ensure integration of the double-deck screen in the same physical space as the single-deck screen.
- New levels of screening efficiency – fewer rejections and significantly higher productivity.
- Movable top deck for easy maintenance.
- Remarkable reduction in greenhouse gas emissions, equivalent in some cases to taking 6,000 cars off the road.
SDRF
Single Deck Roller Feeder
Maximize screening of fines and broken pellets, while standardizing pellet feed to furnaces.
Key benefits:
- Efficient removal of fines and broken particles – improved quality.
- Uniform pellets feed in the furnace-improved productivity and pellet quality.
- Stable operation – less downtime.
- Optimized design for mechanical reliability and ease of maintenance.
- Use of rollers with proprietary anti-wear and anti-sticking coating to increase its lifespan and avoid gap adjustments.
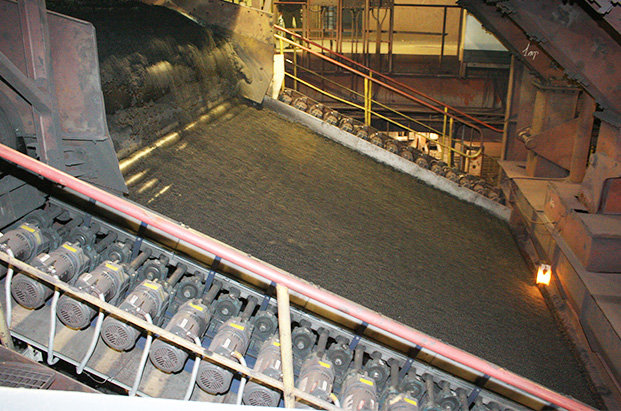
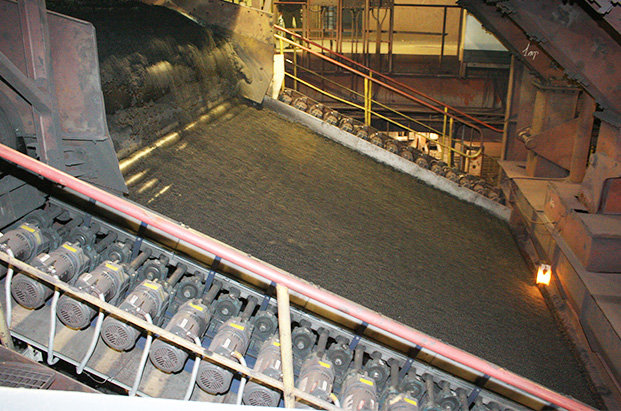
SDRF
Single Deck Roller Feeder
Maximize screening of fines and broken pellets, while standardizing pellet feed to furnaces.
Key benefits:
- Efficient removal of fines and broken particles – improved quality.
- Uniform pellets feed in the furnace-improved productivity and pellet quality.
- Stable operation – less downtime.
- Optimized design for mechanical reliability and ease of maintenance.
- Use of rollers with proprietary anti-wear and anti-sticking coating to increase its lifespan and avoid gap adjustments.
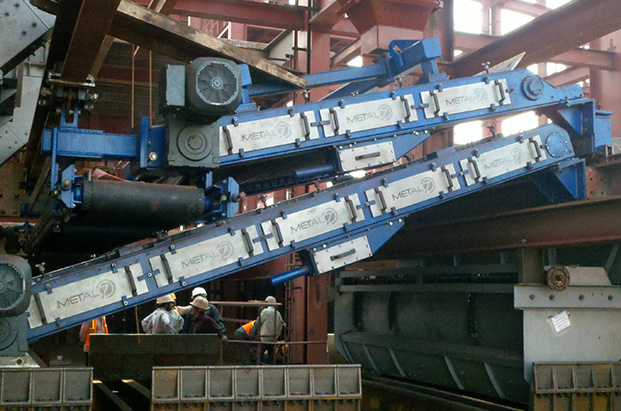
DDRF
Double Deck Roller Feeder
Get the benefits of a single-deck screen for induration furnace feeding, with an extra surface to eliminate oversized pellets. Welcome to productivity, energy savings and quality!
Key benefits:
- Efficient removal of fines and broken pellets to improve quality.
- Removal of oversized pellets for more efficient firing, reducing energy consumption and improving quality.
- Uniform pellets feed into the induration furnace, improving productivity and reducing energy consumption.
- Operational stability with less downtime.
- Optimized design for mechanical reliability and simplified maintenance.
- Use of anti-wear and non-sticking coated rollers to extend the lifespan and avoid frequent re-gapping, ensuring uniform pellets size distribution over time.
DDRF-S
Double Deck Roller Feeder – Segregation
Tangible results confirm it: boost productivity, improve quality, reduce operating costs, and as a bonus, reduce your Scope 1 carbon footprint by the equivalent of 15,000 cars a year!
Key benefits:
- Pellets are fed into the induration machine in two layers.
- Patented Epsilon chute to reduce breakage and deformation of green pellets.
- Significant increase in bed permeability in induration furnaces.
Industrially Proven benefits:
- 7.5% increase in productivity.
- Quality improvement of between 2 and 18%.
- Significant up to 15% reduction in energy consumption in the pellet firing process – reduction in Scope 1 carbon footprint.
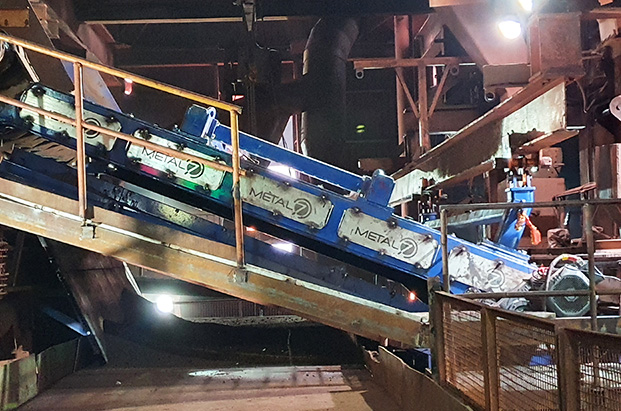
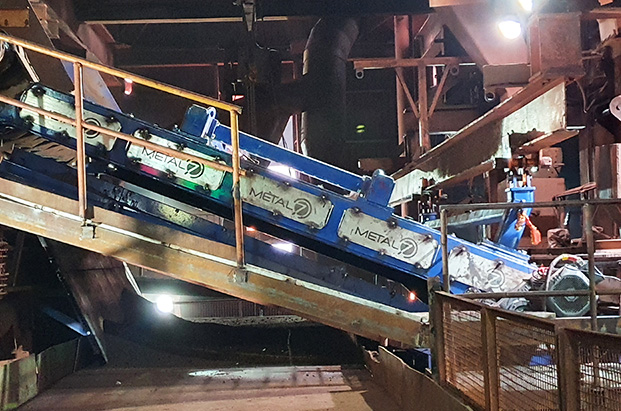
DDRF-S
Double Deck Roller Feeder – Segregation
Tangible results confirm it: boost productivity, improve quality, reduce operating costs, and as a bonus, reduce your Scope 1 carbon footprint by the equivalent of 15,000 cars a year!
Key benefits:
- Pellets are fed into the induration machine in two layers.
- Patented Epsilon chute to reduce breakage and deformation of green pellets.
- Significant increase in bed permeability in induration furnaces.
Industrially Proven benefits:
- 7.5% increase in productivity.
- Quality improvement of between 2 and 18%.
- Significant up to 15% reduction in energy consumption in the pellet firing process – reduction in Scope 1 carbon footprint.
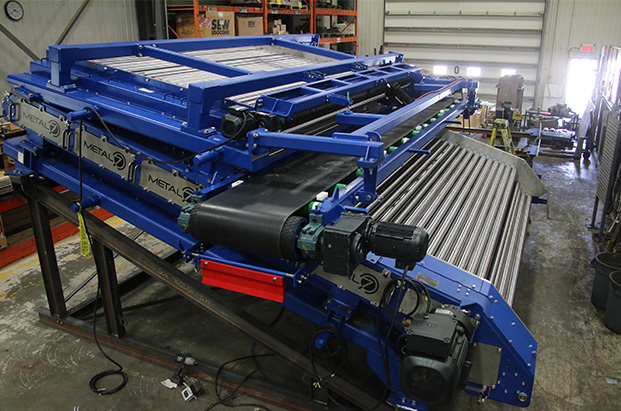
TDRF
Triple Deck Roller Feeder
Increase your plant’s operational efficiency with Metal7’s exclusive revolutionary technology, while reducing the carbon footprint of your pelletizing operations!
Key benefits:
- Pellets are fed into the oven in two layers.
- Patented Epsilon chute reducing breakage and deformation of green pellets.
- Patented triple screening decks design to increase screening area.
- Significant increase in bed permeability in the induration machines.
- Productivity increased by 7.5%.
- Quality improvement up to 18%.
- Significant reduction up to 15% in energy consumption in the pellet induration machines- reduction in carbon footprint associated with Scope 1.