Spanning 2.5 days, Corem’s 5th symposium marked a historic milestone with a remarkable turnout. It proved to be a resounding success, leaving an indelible mark on everyone who participated. The event became the epicenter for key stakeholders in the iron ore pelletizing industry, where they engaged in lively discussions about industry challenges and the future of pelletizing in the era of sustainable steel production.
Metal7 was an integral part of this symposium, contributing two scientific presentations, setting up an informative booth, and even hosting a pre-symposium meeting on the day prior. Engineers and scientists hailing from various iron ore pellet producers, research institutions, universities, and equipment suppliers came together to impart their expertise and foster a vibrant exchange of ideas in the realm of iron ore pelletizing.
At the symposium, we delved into a diverse array of pivotal subjects, such as:
- Feed Preparation: Exploring methods for preparing raw materials.
- Balling Techniques: Discussing the art and science of creating pellets.
- Green Ball Quality and Organic Binders: Analyzing the quality of green pellets and the use of organic binders.
- Green Ball Size Distribution: Examining the distribution of green pellet sizes.
- Induration and GHG Reduction: Addressing induration processes and their role in greenhouse gas reduction.
- Induration Optimization: Strategies for optimizing the induration process.
- Induration Mathematical Modeling: Utilizing mathematical models to improve induration.
- Quality and Simulation of Reduction Processes: Assessing the quality and simulating reduction processes.
- Quality for BF Pellets: Focusing on quality standards for blast furnace (BF) pellets.
- Quality for DR Pellets: Examining quality aspects of direct reduction (DR) pellets.
- Alternatives to Pelletizing: Exploring innovative approaches beyond traditional pelletizing methods.
At this symposium, where experts explored the complexities of greening iron ore pelletizing, we were proud to contribute our insights through two thought-provoking presentations:
- Green Ball Size Distribution – Revolutionizing Iron Ore Pelletizing: The Screening Process Flowsheet of the Future.
- Induration Optimization – Optimizing Roller Screening Performance in Pelletizing Plants: The Benefits of Pellets Segregation in the Firing Process.
We embarked on an exciting journey into crucial aspect of green ball size distribution and induration optimization. Our mission was to uncover how our innovative screening process flowsheet and pellets segregation during the firing process could be the driver of a revolutionary era in the world of pelletizing.
This exciting endeavor incorporates, among other, the extraordinary capabilities of Metal7’s DDRS technology, unleashing a wave of transformation within the industry:
🌱 Optimizing Feed Splitting: We’ve utilized the power of feed splitting to ease the burden on the fines screening zone, leading to a significant enhancement in screening efficiency.
🌱 Enhancing Pellet Quality: Our process ensures a higher yield of near-size pellets in the final product, effectively diminishing recirculating load and resulting in a palpable boost in plant throughput.
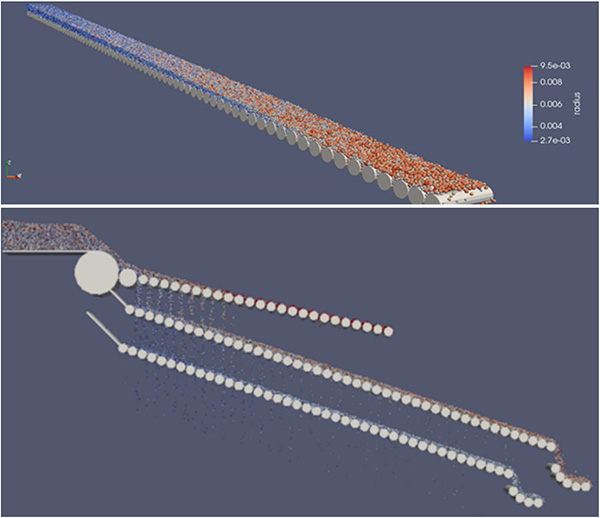
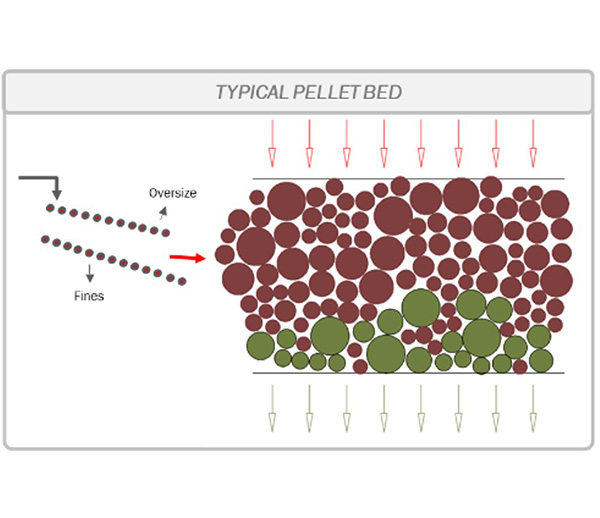
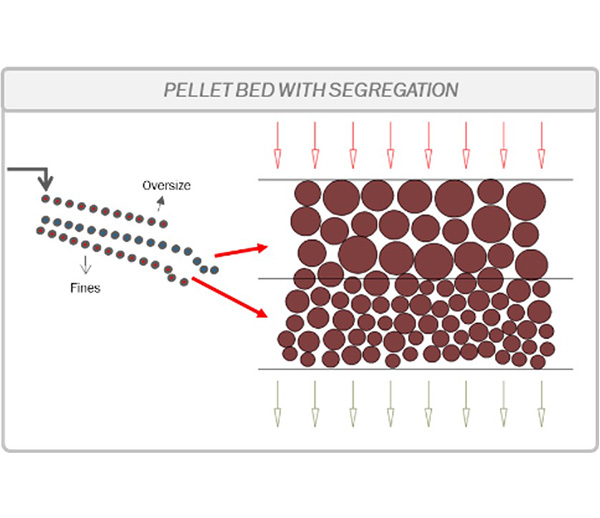
But the innovation doesn’t stop there. We’re also proud of our new DDRF-S and TDRF offerings, both of which are now integrated into the initial segregation (a recent entrant in the market) and our patented Epsilon Chute, boasting an impressive track record of industrial success. This innovation brings with it a myriad of benefits:
🚀 Pellets Segregation Enhancement: Our technology paves the way for efficient pellets segregation inside the furnace, a breakthrough that optimizes the entire firing process.
🚀 Epsilon Chute Design: Our Epsilon Chute is meticulously engineered to reduce pellet velocity and maintain the spherical integrity of pellets, ensuring superior bed permeability, quality, and performance.
🚀 Boosted Productivity: We’ve achieved remarkable productivity gains of up to 7.5%, a testament to our unwavering commitment to pushing the boundaries of what’s possible.
🚀 Energy Efficiency: With energy reductions of up to 15%, our innovations not only benefit the bottom line but also contribute to a more sustainable approach.
🚀 Improved Pellet Quality: Our solutions offer an impressive up to 18% enhancement in pellet quality, further solidifying our dedication to excellence.
In essence, the breakthroughs achieved through DDRS, DDRF-S, and TDRF offer a compelling case for more efficient agglomeration—offering better split, improved sizing, and reduced recirculation. Simultaneously, they champion the cause of more efficient firing by ensuring enhanced bed permeability, advanced segregation, and the game-changing Epsilon Chute.
These innovations, showcased at the symposium, underscore our relentless pursuit of excellence and innovation within the iron ore pelletizing industry.
Our participation and presentations exemplify our commitment to innovation and quality enhancement in the iron ore pelletizing industry, and we were delighted to share our expertise with fellow professionals and thought leaders at this extraordinary event.